When it comes to maintaining and protecting our facilities, we often make the mistake of overlooking the critical aspects, such as the roof. SmartSeal, as a solution, plays an important role in defending against environmental elements. However, through years of wear and tear, they inevitably succumb to damage and need repair or replacement.
That’s where roof coatings come into play. Think of roof coatings as a thick paint, engineered distinctly to restore existing roofs, provide seamless waterproofing, minimize expensive tear-offs, and most importantly, offer significant energy cost savings. These coatings have become undeniably popular, with warranties that typically span between 10 to 20 years.
The variety of roof coating products available in the market cater to diverse needs, making it easier to find a perfect fit for your roofing system. From commercial establishments to residential buildings, roof coatings offer an easy and cost-effective solution for roof restoration and maintenance without having to deal with the hassle and expense of a complete replacement.
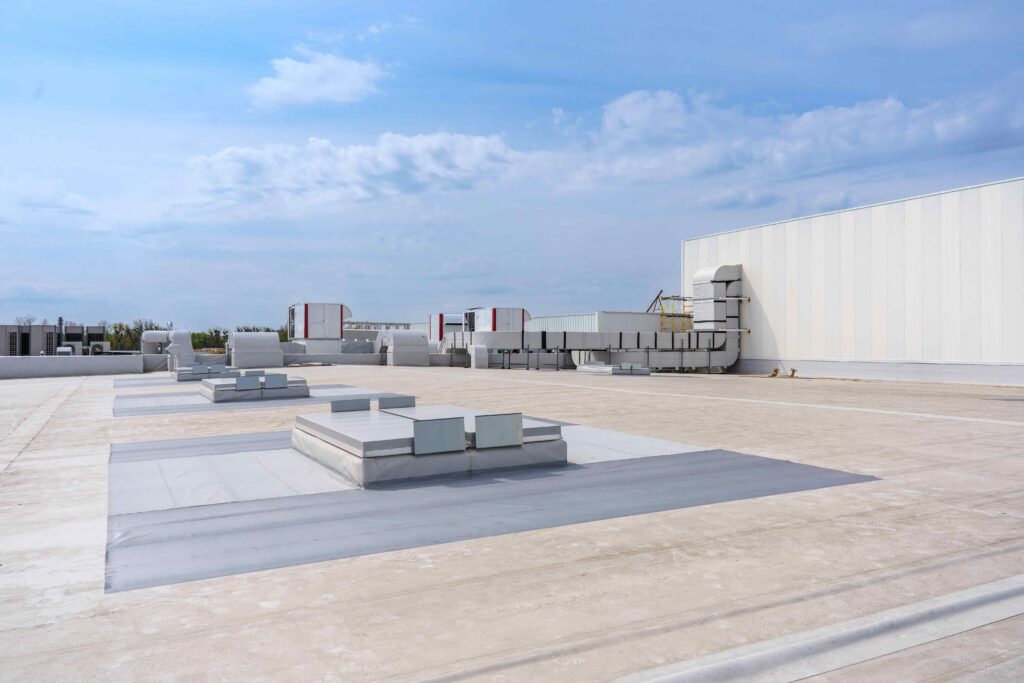
Key Takeaways
- Roof coatings are a cost-effective solution for roof repair and restoration.
- They provide seamless waterproofing, protecting roofs from environmental damage.
- Roof coatings are energy-efficient, leading to significant energy cost savings.
- Various roof coating products cater to diverse needs, ensuring there’s a perfect fit for all roofing systems.
- Roof coatings are accompanied by warranties typically spanning 10 to 20 years, helping secure a long-term investment in your property.
- They play a vital role in regular roof maintenance and can significantly turn down the necessity of a complete roof replacement.
The Benefits of Silicone Restoration Membranes for Roof Longevity
Today, we are seeing a significant shift in the roofing industry towards sustainable solutions. One such solution increasingly relied upon is the Silicone Restoration Membrane (SRM). SRMs offer numerous advantages that extend the longevity of your roof, presenting an ideal solution for commercial proprietors seeking a balance between cost-efficiency and performance. Wholeheartedly embracing the Silicone Restoration Membrane’s power can truly transform your approach to roof leak repair and maintenance. Let’s delve into the benefits of this revolutionary product.
Seamless Waterproofing Solution
Silicone Restoration Membranes are renowned for their excellent waterproofing properties. When applied, the SRM forms an impermeable barrier directly onto the existing roof, encapsulating it to prevent water ingress completely. This unique feature makes it an ideal solution for roof waterproofing, as it not only repairs existing leaks but forestalls the emergence of future ones.
Energy Cost Reduction
Apart from preventing roof leaks, SRM boasts reflective properties that contribute to reducing energy costs. The highly reflective surface repels the sun’s rays rather than absorbing them, leading to a significant decrease in the rooftop temperature. This temperature reduction translates to lower energy costs, as less cooling energy is needed to maintain a comfortable internal temperature, especially during the hot summer months. In this way, SRM helps businesses to become more energy-efficient.
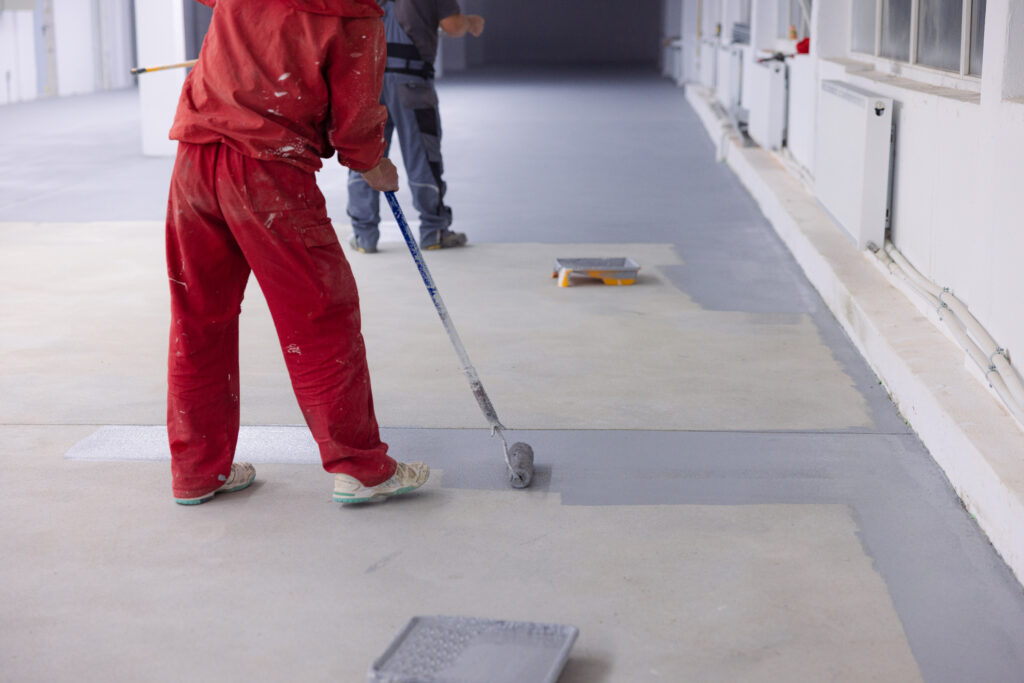
Extension of Warranty Period
A bonus point of using Silicone Restoration Membranes in roof leak repair is the warranty extension. Application of an SRM can renew the warranty of a building’s roof, in some cases extending it by an additional 10-20 years. This offers peace of mind to property owners, as it promises extended protection against potential damages.
Indeed, from seamless waterproofing to energy cost reduction, and extension of warranty periods, the Silicone Restoration Membrane ticks all the boxes for an ideal roof coating solution. It not only ensures durability but also adds a layer of cost and energy efficiency that makes it a popular choice in commercial roof repair and maintenance.
Determining If Your Facility is a Candidate for Roof Coatings
As pivotal as commercial roof coatings are in roof restoration and roof maintenance, they aren’t universally suited for every roofing system. Knowing whether your facility is a candidate for roof coatings demand a detailed evaluation process handled by a professional roofing contractor.
Roof material, condition of the insulation, integrity of the seams, and maintenance history, all play a vital role in determining the compatibility of your roof with roof coatings. To provide a more structured and clear understanding, we present to you a succinct table that delves into these crucial factors:
Roof Material | Condition Of Insulation | Seams Integrity | Maintenance History |
---|---|---|---|
Flat or low slope roofs made from asphalt, modified bitumen, concrete, single-ply membranes, or metal. | If less than 25% of the insulation is wet, it can be rectified with patches. Otherwise, a full roof replacement might be necessary. | Roofs with firm and secure seams that prevent water infiltration are excellent candidates for coatings. | A well-maintained roof paves the way for effective application of coatings. Neglected roofs might require foundational repairs before the application of coatings. |
If your roof checks the above boxes, it stands a strong chance of benefiting from roof coatings. However, it is mandatory to have a professional inspection to confirm its eligibility.
Hiring a professional roofing contractor not only ensures an accurate evaluation but also provides informed guidance on choosing the right coating based on the roof’s current condition and the facility’s weather exposure. Remember, the success of roof sealant application is dependent on the applicability of the coating to your type of roof and how effectively it can work with your existing rooftop environment.
With that said, identifying whether your facility is an ideal candidate for roof coatings is the critical first step towards a successful roof restoration project.
Comprehensive Guide to Roof Coating Types and Their Applications
The commercial roofing market offers a plethora of coating options, each uniquely formulated to cater to different requirements. Whether your roof requires UV protection, weather resistance, or high impact endurance, there is a coating tailored to meet those needs. Let’s delve into the specifics of four popular roof repair coatings: acrylic, silicone, polyurethane, and the relatively new asphaltic rubber membrane system.
Acrylic Coatings: UV Protection and Flexibility
Acrylic coatings are renowned for their excellent UV protection. They significantly reduce surface temperatures, thus minimizing the thermal degradation of your roof. Features like easy application and flexibility make them a preferred choice for many. However, their usage may not be ideal in areas with persistent ponding water.
Silicone Coatings: Durability and Resistance to Ponding Water
For those dealing with regular ponding water, silicone coatings could be your best bet. These roof coatings are durable and exceptionally resistant to weather change. Its ability to withstand ponding water without losing strength makes it a favorite for commercial structures.
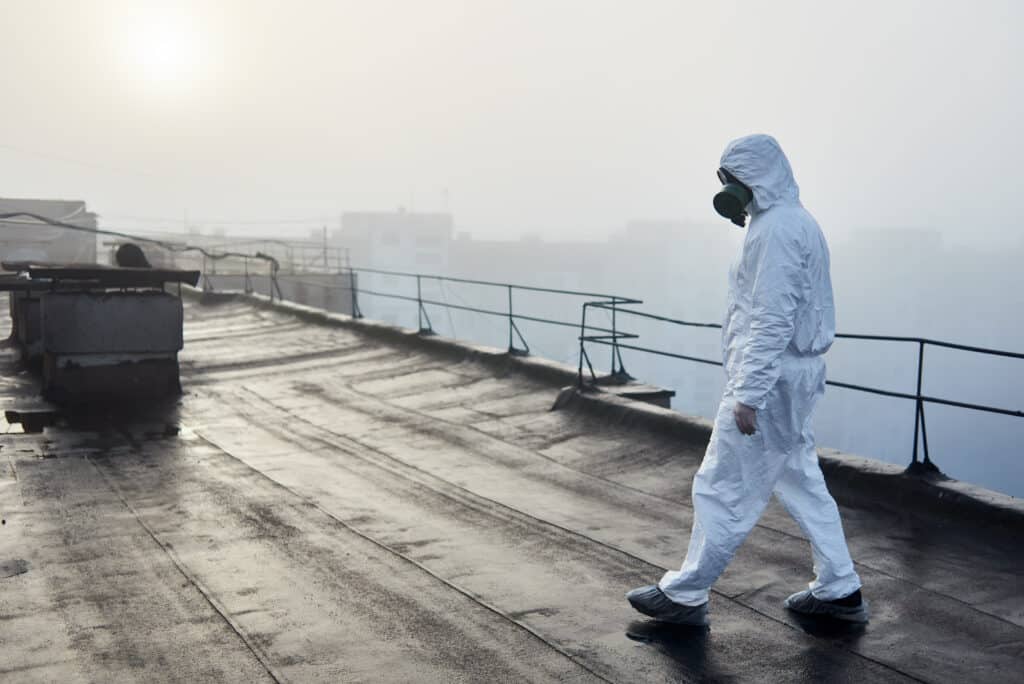
Benefits of Restoring vs. Replacing Your Commercial Roof
When the roof of a commercial building suffers from damage or deterioration, the two most common solutions considered are roof restoration or roof replacement. However, each approach comes with its unique set of benefits and drawbacks. In this section, we will explore the cost-effectiveness, energy savings, and environmental advantages associated with the restoration of commercial roofs using high-quality roof coatings. We hope that this information will assist property owners and managers when making decisions about commercial roof repair and maintenance.
Cost-Effectiveness of Roof Restoration
Roof restoration, particularly when performed using quality roof coatings, can be a significantly more cost-effective solution than a complete roof replacement. The overall expenses associated with restoration are mainly categorized as maintenance, which could potentially result in less tax liability compared to capital expenses involved in a complete roof replacement. Furthermore, restoration can extend the lifespan of a commercial roof by an additional 10-20 years, providing incredible long-term value.
“Cool Roof” Effect and Energy Savings
Another compelling benefit of roof restoration via roof coatings is the potential energy savings due to the ‘cool roof’ effect. High-quality roof coatings are often reflective, bouncing away the harsh UV rays instead of absorbing them. This reflective property helps lower the temperature inside the building, resulting in less need for air conditioning and leading to substantial energy savings in the long run.
Conclusion
As we wrap up our discussion, it’s evident that the strategic application of roof repair coatings offers an effective approach to extending the lifespan of a commercial roof, along with significant cost, energy, and environmental benefits. These coatings form an integral part of a comprehensive roof maintenance strategy and play a pivotal role in enhancing a building’s overall energy efficiency.
From acrylic to silicone, polyurethane, and asphaltic rubber, the diversity of coatings available in the market suits various roofing requirements. The crux is in choosing the most suitable coating that aligns perfectly with the specificities of your roof. We understand that this decision should not be made lightly, which is why seeking professional assessments is a step that can’t be bypassed. These experts can help you make an informed decision, ensuring the long-term success and performance of your roof coating.
Let’s not forget, these coatings are more than just about immediate repair and waterproofing. They contribute significantly towards a building’s performance by promoting energy efficient roofing. This isn’t just about protecting your roof—it’s about creating a more sustainable future, reducing overhead costs, and cultivating an environment that thrives on resourcefulness and efficiency.
Indeed, the right roof restoration measures, bolstered by the appropriate coatings, can form an effective front against roof decay while simultaneously leveraging the benefits of energy efficiency. Through such strategic decisions, we can foster a healthy balance between building maintenance, cost-efficiency, and environmental conservation.
SmartSeal leads the way for exceptional commercial roof coating in Leesburg, FL. Reach out now to begin your project with us.
FAQs
What are roof coatings and how do they contribute to roof repair?
Roof coatings are engineered solutions, often likened to thick paint, designed to restore existing roofs, provide seamless waterproofing, protect against leaks, and offer potential energy cost savings. They are specifically designed to extend the lifespan of your roof, reducing the need for frequent replacements.
What is a Silicone Restoration Membrane (SRM) and how does it benefit roof longevity?
A Silicone Restoration Membrane is a fluid-applied coating that is sprayed directly onto the existing roof. As it provides a seamless waterproofing solution, it’s ideally suited for commercial roofs with fair to good underlying conditions. They are energy-efficient, resist UV rays, and can significantly extend the life of a roof.
How can I determine if my facility is a candidate for roof coatings?
A professional roofing contractor should assess the existing roof system. Considerations include the roof’s material, the condition of the insulation, integrity of seams, and whether maintenance has been regular. The ideal candidates are roofs with a flat or low slope, which might include materials like asphalt, modified bitumen, concrete, single-ply membranes, and metal.
What are some different types of roof coatings and their applications?
The commercial roofing market offers various types of coatings, each with unique properties suitable for different applications. This includes acrylic coatings for UV protection, silicone for weather resistance and ponding water tolerance, polyurethane for impact resistance and foot traffic, and the recently developed asphaltic rubber membrane system for cost-effective service life extension.
Can you describe the Silicone Restoration Membrane installation process?
Installation starts with an infrared inspection to identify any wet insulation. Then, saturated areas are replaced, and the roof surface is power-washed to eradicate contaminants. Next, the roof’s seams are reinforced before applying the membrane across the roof to create a seamless, waterproof barrier.
What are the benefits of restoring vs. replacing a commercial roof?
Roof restoration offers cost-effectiveness, extended roof life, reduced energy costs due to the ‘cool roof’ effect, and environmental advantages like avoiding disposal of old roofing material. The financial aspect can be substantial as roof restoration expenses can be categorised as maintenance, potentially reducing tax liabilities.
What steps should be taken before applying roof repair coatings?
Evaluation and preparation are crucial before the application. An infrared inspection is first conducted to detect any underlying damage, especially moisture. Then these areas are addressed, and the surface is power-washed for optimal adhesion of the coating. Reinforcing the seams ensures the longevity and durability of the repair.
How does regular roof maintenance play a role in the longevity of the coating?
The effectiveness of roof repair coatings is heavily influenced by regular, quality roof maintenance. Maintenance involves regular inspections, cleaning, and minor repairs as needed, which helps preserve the integrity of the roof system and prolongs the effectiveness of the roof coatings.
How do roof coatings enhance energy efficiency and building performance?
Certain coatings have high reflectivity and UV resistance, which can lower the roof’s surface temperature, reducing the heat transferred into the building. This leads to lower energy costs and more stable interior temperatures, improving facility temperature regulation and comfort.
How do I select the correct roof repair coating for my specific roof type?
Coatings can match various roofing systems, including TPO, EPDM, and PVC, each valued for their respective properties. Working with knowledgeable manufacturers and roofing professionals ensures a compatible product is chosen that aligns with the building’s requirements and budget constraints.